Lytron joins Boyd
Boyd announced the acquisition of Lytron Inc. on July 24, 2019 to further augment Boyd’s robust global manufacturing organization and engineering capacity for liquid cooled solutions. We’ve been working hard to integrate these two complementary product lines to streamline your customer experience. The Lytron operating brand has been retired and is now part of Boyd. For more information on Boyd’s acquisition of Lytron, please see the press release here:
We’re proud to offer the same great products that you’ve purchased from Lytron in the past – and happy that you now have access to the Thermal, Sealing and Protection solutions from our broad portfolio. Please see the below quick links to view legacy Lytron products and calculators:
Check our Chiller and Cooling System Service Tools page for software and manual downloads.
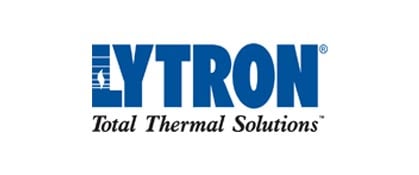
Liquid Cooling System Service
We stand behind our liquid cooling systems and expect them to perform reliably for you over many years. Achieving this long tenured, reliable performance does require regular maintenance to assure peak performance.
We’re responsive to customer support needs ranging from spare parts fulfillment, system service, and repair solutions. Globally available service operations and factory-certified technicians provide rapid, effective, and affordable service to minimize system maintenance downtime.
Have questions? We’re ready to help!